As the automotive industry embraces digitalization and electrification, Mercedes-Benz Berlin-Marienfelde is emerging as a global center for manufacturing innovation. The historic plant is redefining production through advanced technologies, sustainability, and digital integration, setting new benchmarks for efficiency and automation.
Central to this transformation is the Mercedes-Benz Digital Factory Campus (MBDFC), established in 2022. Positioned as the company’s global competence center for digital production, the campus is anchored by MO360—Mercedes-Benz’s cutting-edge digital production ecosystem. This platform integrates real-time data, AI-powered automation, and next-generation robotics to revolutionize the manufacturing process.
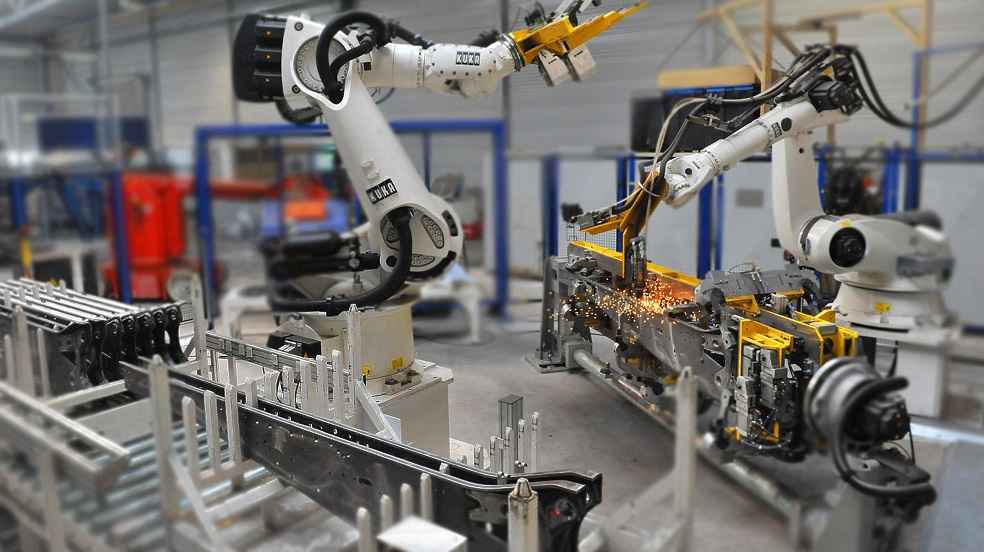
Berlin-Marienfelde now serves as a proving ground for breakthrough technologies before they are deployed across Mercedes-Benz’s global production network. Notably, the facility supported the readiness of the Rastatt plant for the rollout of the new Mercedes-Benz CLA, the first model to feature the new Mercedes-Benz Operating System (MB.OS).
A key innovation at the site is the integration of humanoid robots developed by US-based Apptronik. These advanced machines, including Apollo, are being trained to perform tasks such as transporting components, assisting in assembly, and conducting quality checks. By transferring real-world skills to these robots through teleoperation and augmented reality, the company aims to achieve autonomous robotic operations that enhance flexibility and precision on the production line.
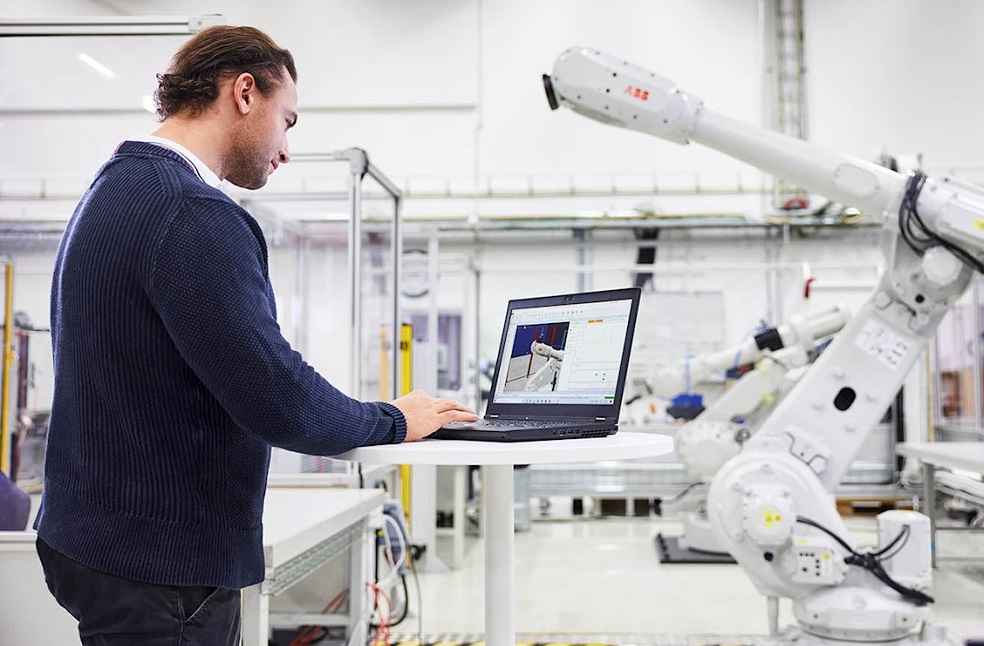
AI is also at the forefront of transformation. The MO360 AI Factory equips employees with real-time analytics, predictive insights, and automated troubleshooting tools. A multilingual chatbot ecosystem offers immediate access to production data and maintenance knowledge, while a virtual multi-agent system identifies and resolves quality deviations with speed and accuracy.
The Berlin plant will begin producing axial-flux electric motors next year. These compact, high-efficiency motors outperform conventional designs in torque density and energy efficiency, making them ideal for next-generation electric vehicles. The manufacturing process includes 100 steps—65 new to Mercedes-Benz and 35 new to the industry—supported by innovations such as AI-assisted assembly and laser-based technologies. The project has already led to over 30 patent filings.
EV WORLD | Cadillac CT4 and CT5 to Go Electric as the Brand Accelerates Electrification