BMW Group’s latest facility at Debrecen in Hungary marks a significant leap forward in sustainable automotive production. This new paint shop, the first of its kind in the company’s global network, operates entirely without fossil fuels, establishing a groundbreaking model for future manufacturing sites.
The Debrecen plant, a 33,000-square-meter state-of-the-art facility, has been designed with a capacity to process 30 vehicle bodies per hour, with room for future expansion. As BMW’s Neue Klasse vehicles prepare for pre-series production, the facility will showcase advanced processes that exemplify top-tier automotive engineering. Expertise gathered from across BMW’s global network has been meticulously applied, driven by the guiding principles of the BMW iFACTORY.
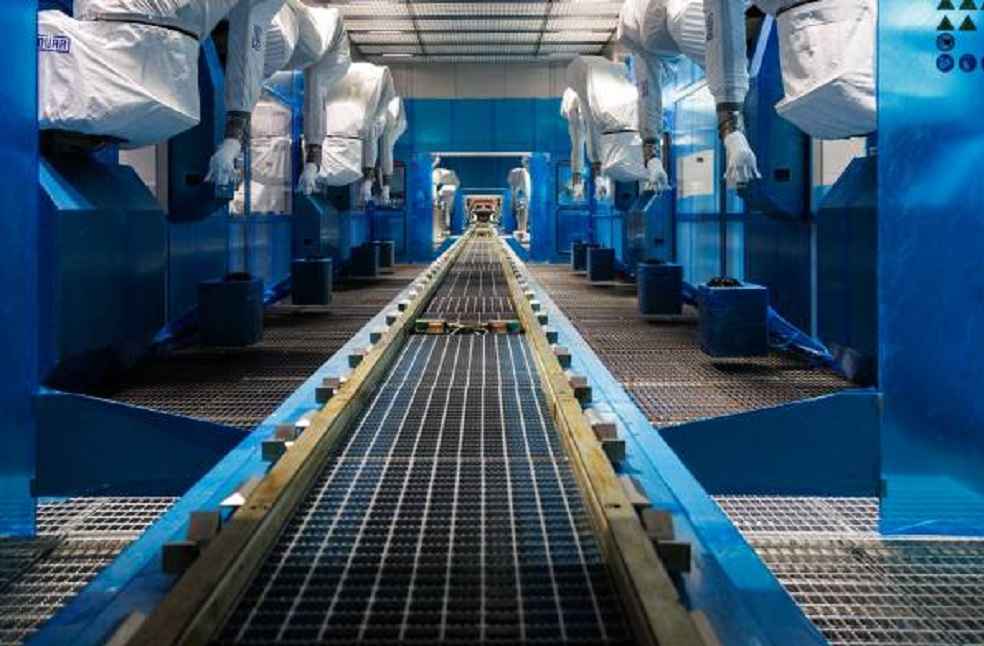
A central innovation at this plant is the power-to-heat principle, which eliminates reliance on natural gas by powering essential processes with electricity. This transition results in a substantial reduction of the plant’s carbon footprint, with all energy sourced exclusively from renewable origins, reinforcing BMW’s dedication to environmental stewardship.
The Heat Grid project further enhances energy efficiency, consolidating waste heat from various processes into a multivalent storage boiler, leading to energy savings of up to ten percent. Operating at a reduced water supply temperature of 65 degrees Celsius—a significant improvement from traditional systems—this project represents a remarkable advance in energy management.
The Debrecen plant also features the innovative eRTO process for exhaust air purification, which operates at temperatures up to 1,000 degrees Celsius using electricity alone. This cutting-edge method effectively incinerates solvent residues, delivering exceptional energy efficiency and high thermal recovery.
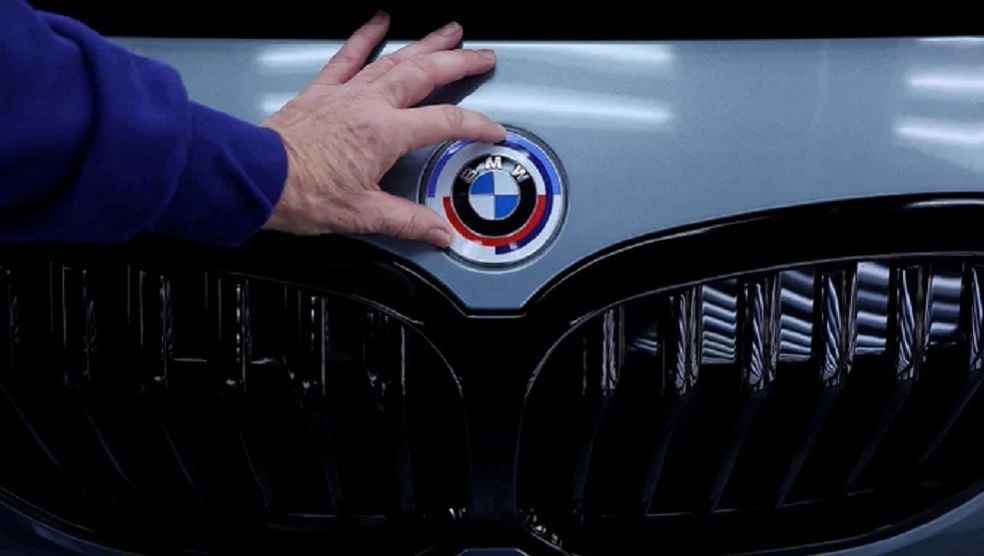
The plant’s environmental commitment shines through its use of dry separation technology, which filters out paint overspray while significantly reducing water consumption. This method allows up to 90 percent recirculating air within the spray booths, with stone powder used in filtration finding new life in industries like cement manufacturing, reducing waste and promoting sustainability.
Digital technology underpins the entire operation, with Automated Guided Vehicles (AGVs) seamlessly moving car bodies through the production line, and Automated Surface Inspection (AOI) systems, powered by artificial intelligence, detecting and addressing any irregularities post-painting. The planning and training for this facility were conducted entirely in a virtual environment, showcasing BMW’s forward-thinking approach to modern manufacturing.
AUTO TECH | Global Auto Alliances Challenge Indian IT ER&D Amid Shifting Industry Trends