As the automobile industry pivots towards sustainability, car manufacturers are exploring inventive ways to repurpose waste along with plastic recycling. Ford, Audi, and Volkswagen are now embracing the circular economy, driven by two significant needs: reducing new resource consumption for plastic production, and mitigating plastic waste accumulation from used products.
A wealth of plastic within modern vehicles presents substantial opportunities for recycling. For example, the Ford Bronco Sport integrates wiring harness clips crafted from recycled plastic sourced from recovered fishing nets. Alper Kiziltas, Ford’s technical expert, suggests that as much as 700 lbs. of plastic per vehicle might be generated from recycled materials shortly, with close to 10 percent originating from repurposed fishing net material.
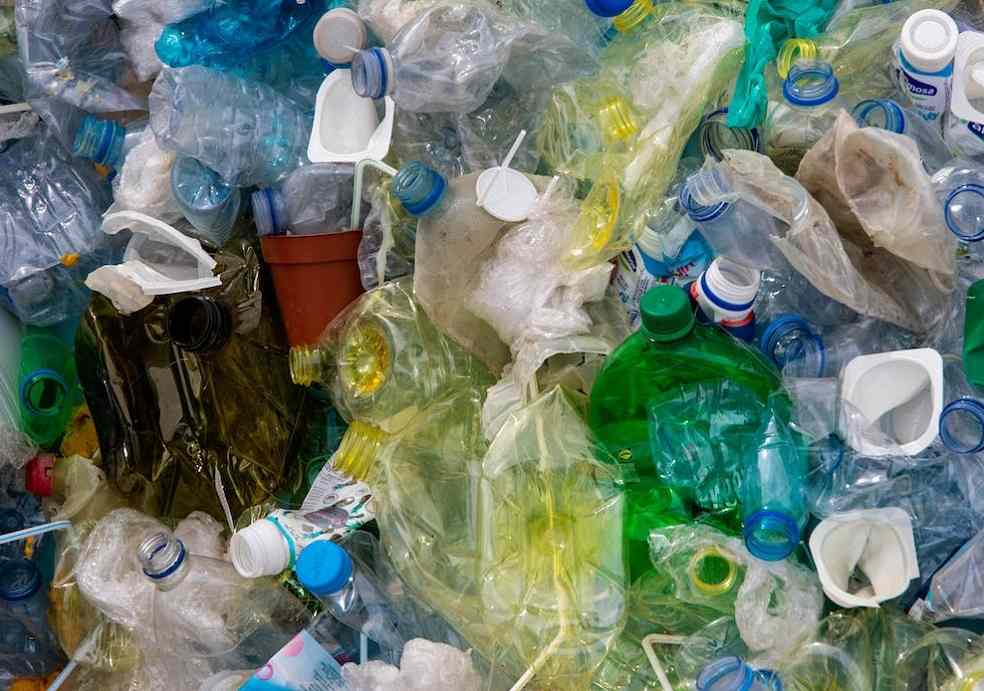
The environmental impact of these strategies is especially palpable within car interiors. Audi, in partnership with polymer products titan LyondellBasell, produces plastic seat belt buckle covers for its Q8 e-tron EV using plastic recovered from parts of wrecked Audis. This partnership forms part of the PlasticLoop project, a pioneering venture seeking to establish a closed-loop process for recycling automotive plastic waste into new vehicles.
Additionally, Audi harnesses polyethylene terephthalate (PET) plastic from disposable bottles. This PET combines with leftover textiles and fabric selvages collected from manufacturing plants, resulting in a novel fabric named ‘Kaskade’. With the texture and feel of natural fiber materials such as wool, Kaskade’s blend comprises 15 percent selvage material, 35 percent PET, and 50 percent new polyester. The concoction guarantees a fabric with an uncompromised aesthetic and tactile experience.
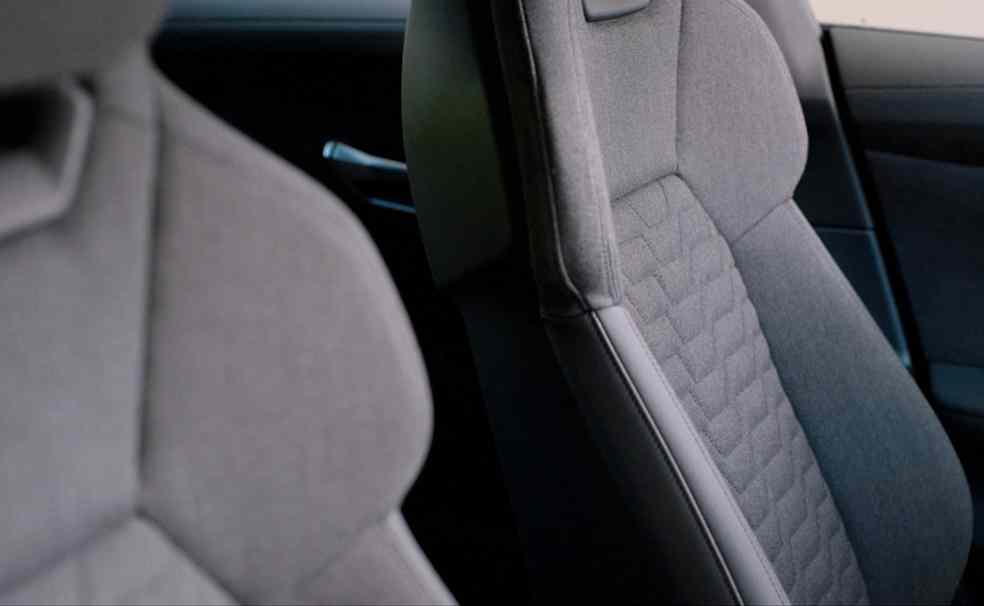
Audis’ e-tron GT also employs Econyl for carpeting and floor mats, a substance derived from 100 percent recycled nylon fibers originating from manufacturing waste, fabric scraps, and discarded fishing nets. Regardless of the innovative approach, the transition toward a circular economy faces hurdles. The financial cost of recycled materials surpasses that of virgin materials, although energy consumption remains similar, thus not impairing efficiency.
Faurecia, an industry supplier, has created the ‘Seat for the Planet’ project, resulting in a seat that is approximately 15 percent lighter than conventional ones. Composed of bio-sourced or recycled materials, the design is crafted for easy separation of materials for future recycling. An integral part of this project is the introduction of ‘Auraloop’, a cushioning material developed in collaboration with Thai chemical company Indorama Ventures. Auraloop, a recyclable polyester-based fiber structure, promises enhanced comfort, durability, and energy efficiency compared to conventional polyurethane.
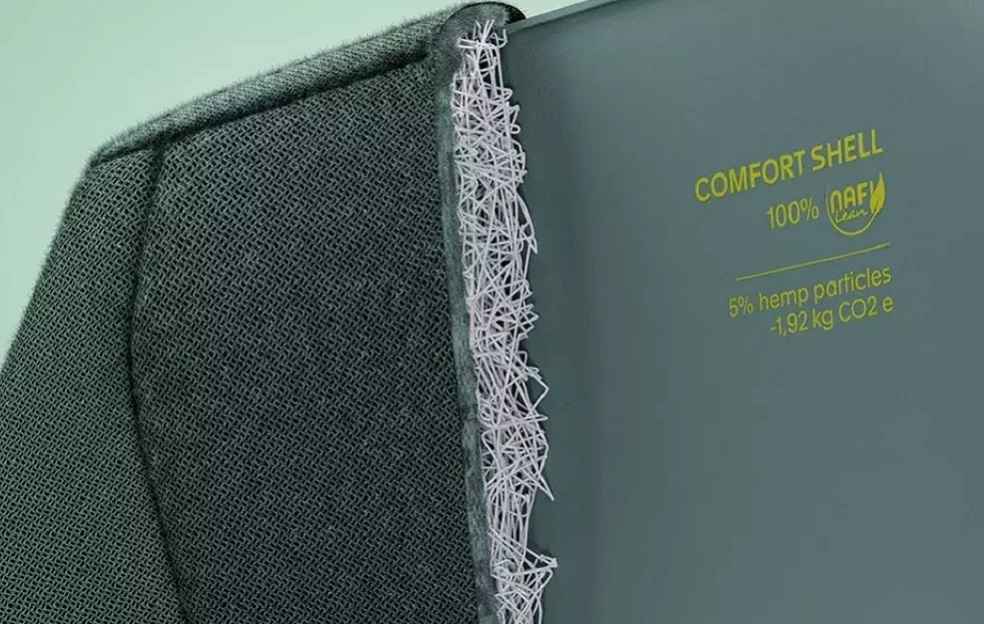
On a different track, Volkswagen investigates the substitution potential of non-plastic elements within automotive interiors. The company experiments with fibers recovered from recycled paper as an alternative to natural fibers in components like map pockets on door panels.
Despite such pioneering strategies, variables such as logistics, supply chain length, cost, and quality consistency pose challenges. Notwithstanding these hurdles, these initiatives exemplify a profound transformation in the automotive industry’s approach to waste, indicating an intensifying commitment to environmental stewardship and ecological sustainability.
EV WORLD | Ballard and Ford Trucks Alliance: Fuel Cell Revolution in Heavy-Duty Transport