Advancing its digitalization efforts, Audi, the distinguished automotive powerhouse, has launched an artificial intelligence (AI) system to monitor the quality control of spot welds in car manufacturing. This innovative initiative was initially developed and trialed at Audi’s Neckarsulm site, symbolizing a crucial implementation step for the Audi-launched Automotive Initiative 2025 (AI25).
Leveraging AI, Audi can now scrutinize roughly 1.5 million spot welds on 300 vehicles during each shift at the Neckarsulm site. This significantly surpasses the previous manual monitoring system, which employed ultrasound-based random analyses to examine around 5,000 spot welds per vehicle. The new AI system enables employees to concentrate on potential anomalies, thus facilitating a more efficient, targeted quality control approach.
Preparations are underway to extend this AI application to other Volkswagen Group plants. The installation of the necessary AI technical infrastructure is currently in progress at Audi Brussels, with similar initiatives scheduled for the Volkswagen plant in Emden and Audi’s headquarters in Ingolstadt within the year. An expert team is identifying the specific variations in weld settings at these locations to refine the AI model appropriately.
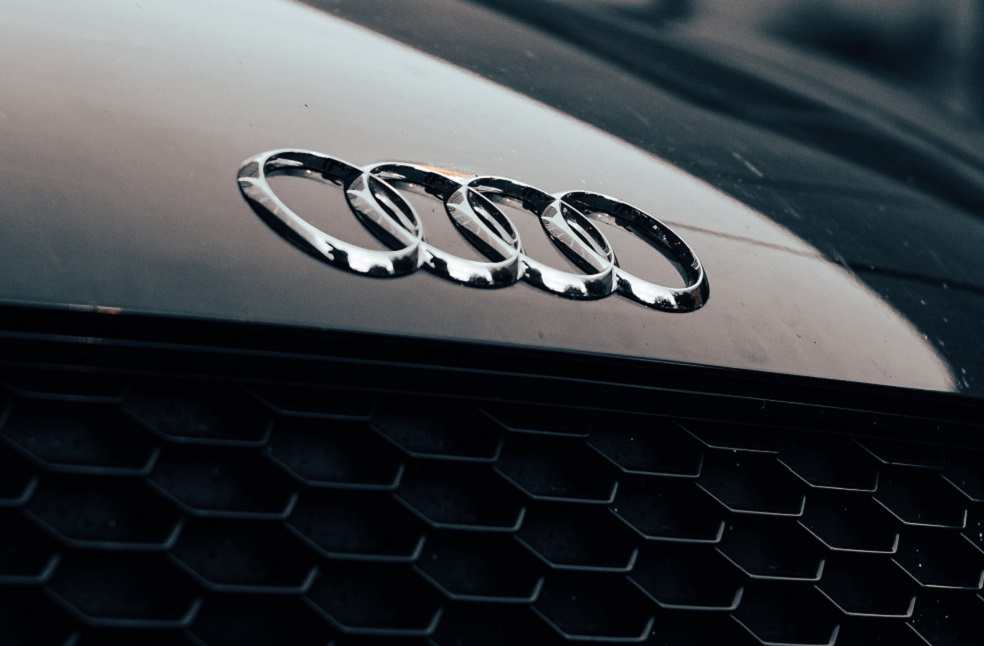
Audi is also looking towards prospects, considering the utilization of AI-generated data to improve other processes, particularly in the field of predictive maintenance. Gerd Walker, Audi Board Member for Production and Logistics, underscored the crucial role of AI in Audi’s production strategy. He remarked, “Digitalized assembly lines are a foundation for Audi’s vision for the production of the future: As part of our 360factory production strategy, we will make production at Audi locations worldwide even more efficient. In this regard, the use of artificial intelligence in series production promises huge potential.”
The development process at the Neckarsulm site was implemented in close coordination with the German Association for Quality (DGQ), the Fraunhofer Institute for Industrial Engineering (IAO), and the Fraunhofer Institute for Manufacturing Engineering and Automation (IPA). This cooperative effort was aimed at making the process audit- and certification-proof, especially given the current lack of independent AI application standards or certifications.
Mathias Mayer and Andreas Rieker, project managers for WPS-Analytics, emphasized the transformative impact of AI, stating, “This means that, for example in manufacturing, it is possible to conclusively demonstrate how the result of an AI-based test comes about.” Alongside the Fraunhofer Institutes IAO and IPA, Audi has developed a production-focused AI guide.
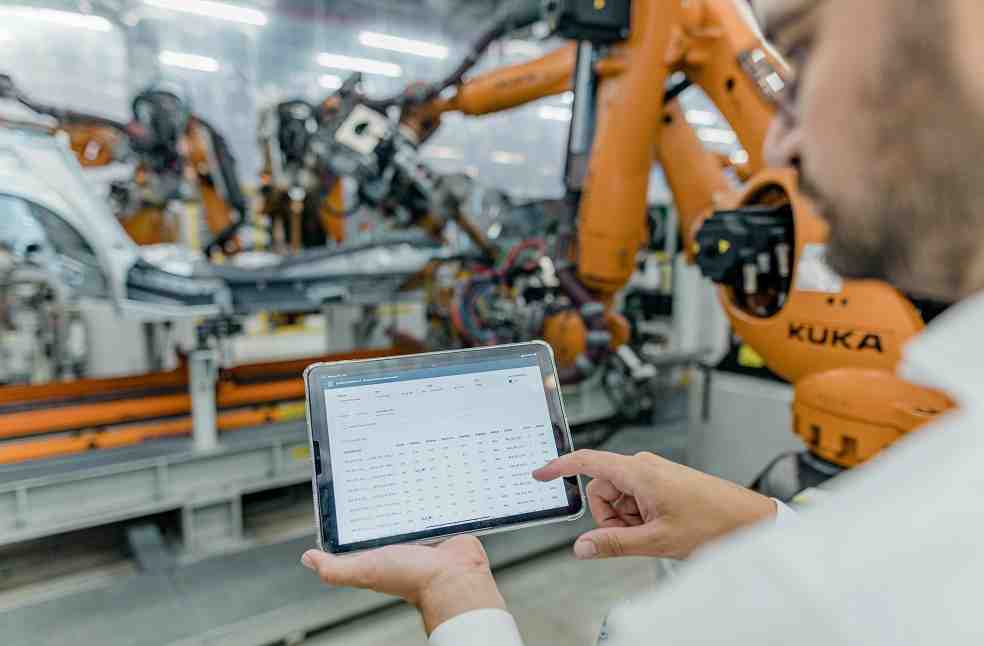
Audi’s AI initiative aligns with the broader Automotive Initiative 2025 (AI25), aiming to build a network of competence for digital factory transformation and innovation. Audi is steadfast in its goal to leverage digitalization to increase production and logistics flexibility and efficiency. Partnering with science and IT industry collaborators, Audi tests digital solutions in a real manufacturing environment at the Neckarsulm site, aiming for later series production deployment. This initiative marks a significant step in Audi’s journey to becoming a ‘smart factory.’
AUTO TECH: Blockchain In Automotive Industry