Mercedes-Benz has launched Europe’s first battery recycling plant with an integrated mechanical-hydrometallurgical process, making it the first carmaker globally to close the battery recycling loop within its own facility. Located in Kuppenheim, Germany, the plant establishes a circular economy for battery materials and supports the company’s sustainability efforts by reducing the need for primary resources.
The facility is designed to recover over 96 percent of valuable materials, including lithium, nickel, and cobalt, which can be reused in new batteries for future electric vehicles. The company has invested tens of millions of euros in the project, enhancing value creation in Germany.
At the plant’s opening, Federal Chancellor Olaf Scholz and Baden-Württemberg’s Environment Minister Thekla Walker praised Mercedes-Benz’s leadership in sustainable automotive practices. Scholz stated, “The circular economy is a growth engine and, at the same time, an essential building block for achieving our climate targets! I congratulate Mercedes-Benz for its courage and foresight shown by this investment in Kuppenheim. Germany remains a cutting-edge market for new and innovative technologies.”
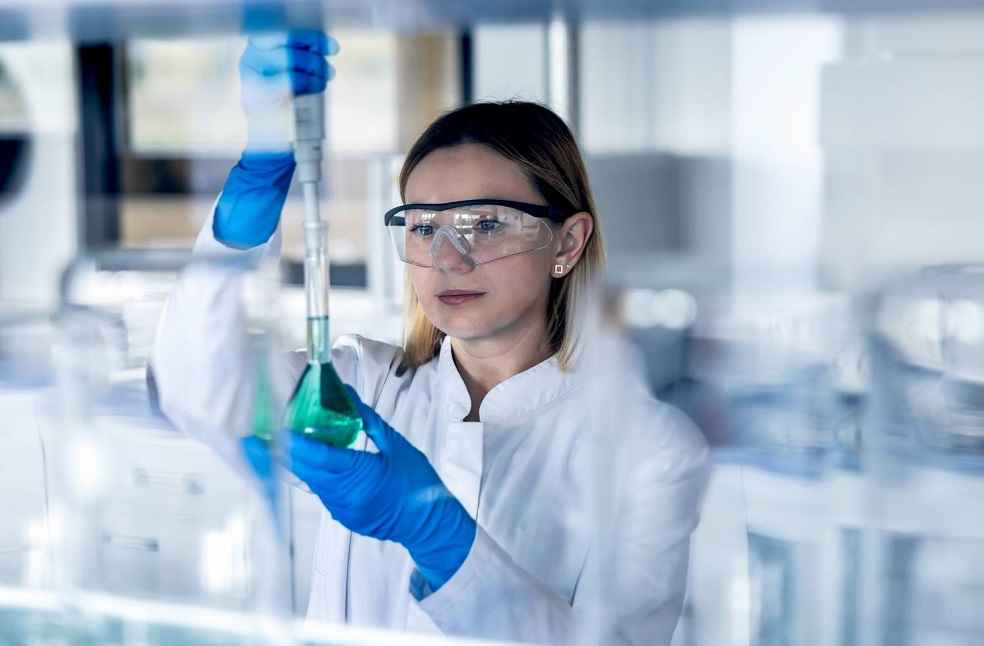
Mercedes-Benz’s technology partner, Primobius—a joint venture between SMS group and Neometals—collaborated on the project, which is part of a research initiative funded by the German Federal Ministry for Economic Affairs and Climate Action. The project explores the entire battery recycling process chain, aiming to scale the industry across Germany.
Innovative Recycling Process
The Kuppenheim plant handles all stages of the recycling process, from shredding battery modules to extracting valuable materials through hydrometallurgy. This method is less energy-intensive and more efficient than traditional recycling techniques, allowing key materials to be reused in new batteries. The facility operates on 100 percent green electricity and is carbon-neutral, aligning with Mercedes-Benz’s sustainability targets.
With an annual capacity of 2,500 tonnes, the recovered materials will support the production of over 50,000 battery modules for new Mercedes-Benz models.
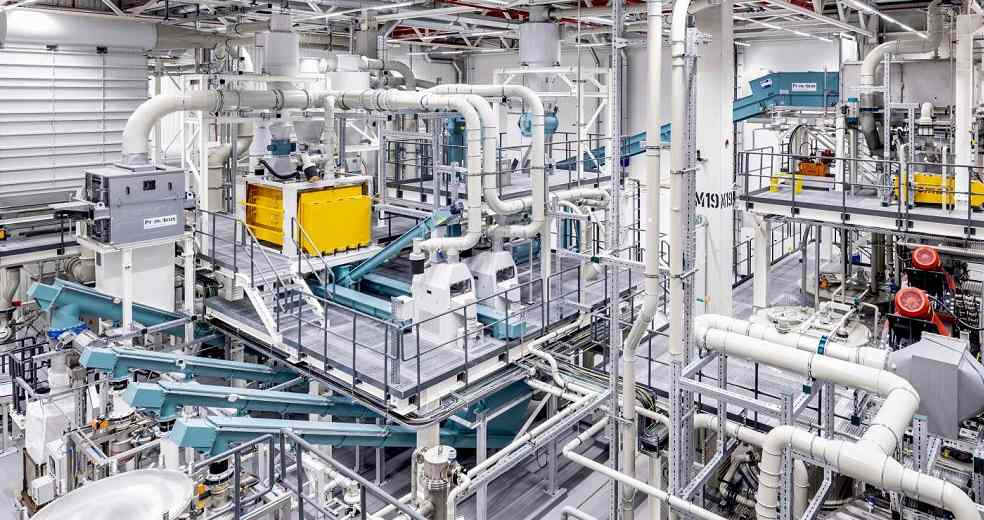
Holistic Sustainability Approach
Mercedes-Benz’s ‘Design for Circularity’ strategy ensures the entire battery lifecycle is considered, from production to recycling. The eCampus in Stuttgart, opened in 2024, integrates this approach into new battery cell development. The company also offers second-life applications for used batteries through Mercedes-Benz Energy, further contributing to resource conservation.
Jörg Burzer, Member of the Board for Production at Mercedes-Benz, highlighted the significance of the plant: “The innovative technology enables us to recover valuable raw materials from the battery with the highest possible degree of purity. This turns today’s batteries into tomorrow’s sustainable mine for raw materials.”
AUTO TECH | China’s Auto Industry Drives Forward with Intelligent Vehicle Innovations