Scania has become the first truck manufacturer in the world to successfully integrate reused components directly into its main assembly line. This move happened in Sweden earlier this year as part of the iReGear research project, carried out in collaboration with KTH Royal Institute of Technology and Scandinavian Transmission Service AB, with funding from Vinnova, Sweden’s innovation agency.
The project focused on remanufacturing a gearbox, which underwent the same stringent quality and functionality checks as gearboxes made entirely from new materials.
Tested on Scania’s regular production line, the gearbox met over 100 quality parameters, proving it was just as good as a newly manufactured one. This achievement demonstrated that remanufactured components can match the quality and performance of brand-new parts, setting a new standard for the industry.
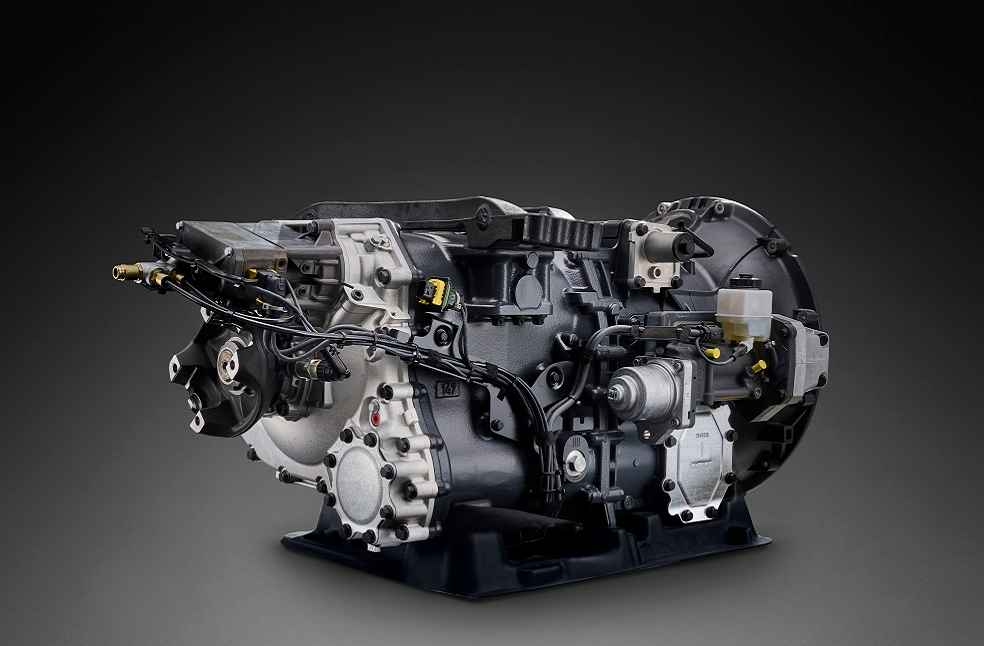
One of the key advantages of this remanufacturing process is its environmental impact. By reusing parts, the remanufactured gearbox used approximately 50% less material and produced 45% fewer carbon emissions compared to manufacturing one from scratch. This approach is not only sustainable but also supports the goal of transitioning to a circular economy, where resources are reused rather than discarded.
Remanufacturing involves taking old, worn-out parts and restoring them to an as-good-as-new condition. Although this process is recognized as having great potential for reducing waste and emissions, it has mainly been limited to producing spare parts for aftermarket purposes in the European automotive industry.
The iReGear project aims to change this by showing it is possible to integrate these reused parts directly into new vehicle production lines, making a big step toward a cleaner, more sustainable future for the transport industry.
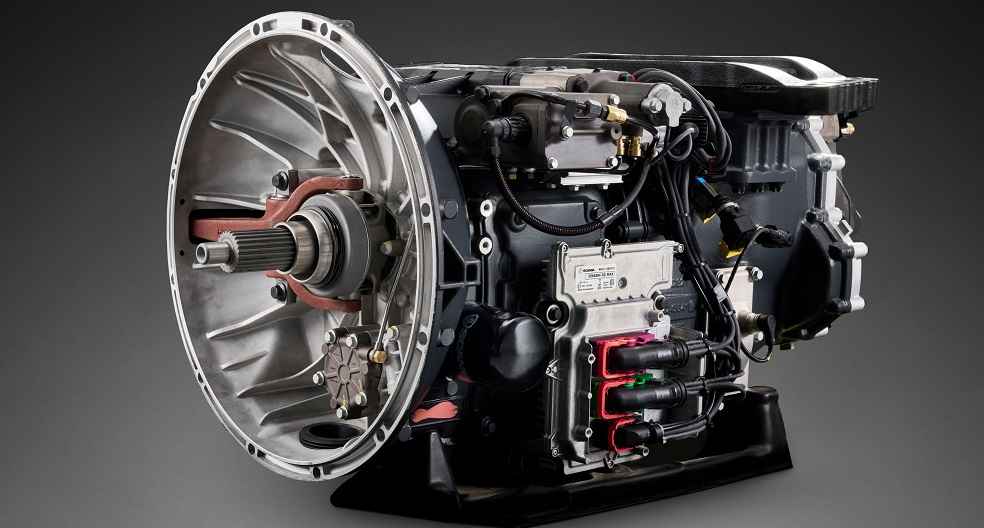
Fredrik Nilzén, Head of Sustainability at Scania, praised the achievement, stating, “What an achievement by the project and everyone involved. This remanufactured gearbox is a compelling example of how the manufacturing of heavy vehicles can become more sustainable, circular and efficient, while still retaining the highest quality standards.”
The project partners believe this breakthrough could pave the way for a broader adoption of remanufacturing in the truck industry and beyond. Assistant Professor Farazee Asif from KTH highlighted that the research provides solid proof that integrating new and remanufactured parts is not only feasible but also essential for developing sustainable manufacturing systems.
Ola Stålebo, CEO of Scandinavian Transmission Service AB, also emphasized the importance of the achievement. “It’s amazing to be able to challenge the old perception that remanufactured parts can only be used for aftermarket purposes. This project shows that with collaboration and innovation, sustainable technology can become a reality.”
DON’T MISS | California Governor Vetoes Bill Mandating Speeding Alerts in New Vehicles